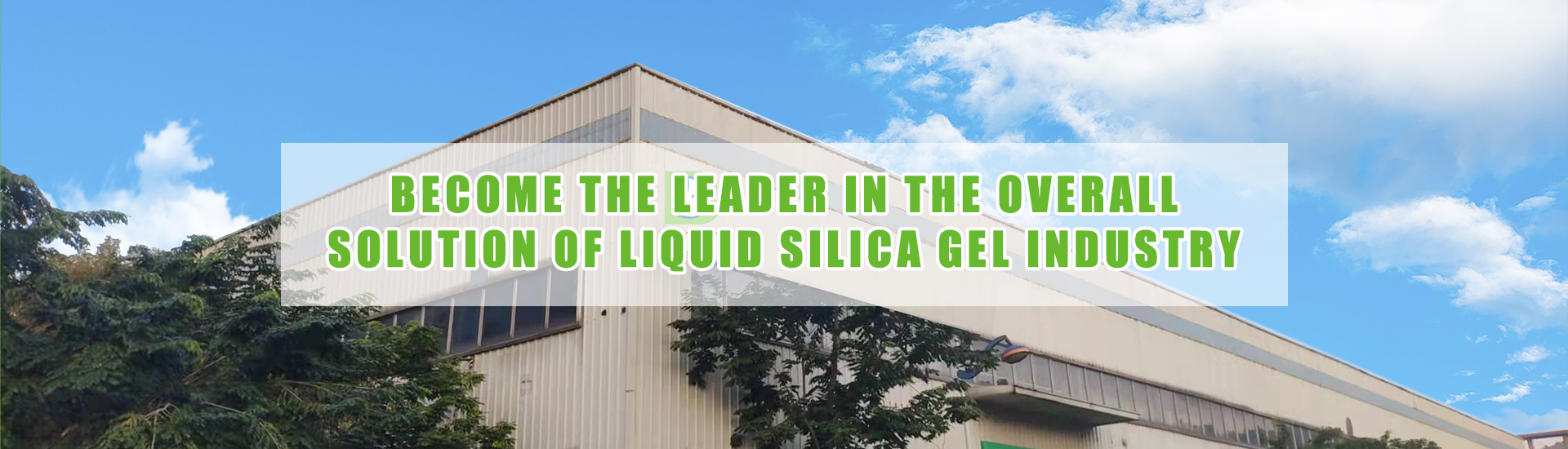
Injection molding machine failure:
Classification of fault parts: 1. According to the status of the fault, it can be divided into:
(1) Gradual failure. Due to the gradual deterioration of the initial performance of the injection molding machine, most of the failures of the injection molding machine belong to this kind of failure. Such failures are closely related to wear, corrosion, fatigue and creep of electrical controls, hydro-mechanical components.
(2) Sudden failure. It is caused by various unfavorable factors and unexpected external influences beyond the limit that the injection molding machine can bear. For example: the screw is broken due to the overload of the barrel entering the iron; the electronic board of the injection molding machine is broken down due to the high pressure intrusion. Such failures often occur suddenly, without any prior indication.
Sudden failures often occur in the use stage of injection molding machines, often due to defects in design, manufacturing, assembly, materials, etc., or operational errors and illegal operations.
2. According to the nature of the fault, it can be divided into:
(1) Intermittent failure. The injection molding machine loses some functions in a short period of time, and it can be restored after a little repair and debugging without replacing parts.
(2) Failure. Some parts of the injection molding machine are damaged and need to be replaced or repaired to return to service.
3. According to the degree of influence of the fault, it can be divided into:
(1) Complete failure. The function of the injection molding machine is completely lost.
(2) Local failure. Cause some functions of the injection molding machine to be lost.
4. According to the cause of the failure, it can be divided into:
(1) Wear failure. Failure caused by normal wear and tear of the injection molding machine.
(2) Misuse fault. Malfunctions due to operational errors and improper maintenance.
(3) Inherent weak faults. Due to design problems, injection molding machines have weak links and failures in normal use.
5. According to the risk of failure, it can be divided into:
(1) Dangerous failure. For example, the safety protection system loses its protective function when needed, causing personal injury and failure of the injection molding machine; failure caused by the failure of the hydraulic electronic control system, etc.
(2) Safety failure. For example, the safety protection system operates when it is not required; the injection molding machine fails to start when it cannot start.
6. According to the occurrence and development law of injection molding machine failures, it can be divided into;
(1) Random failure. The timing of failures is random.
(2) There is a rule failure. There are certain rules for the occurrence of failures.
Each type of failure has its main characteristics, the so-called failure modes or states. The fault states of various injection molding machines are quite complex, but can be summarized as follows: abnormal vibration, mechanical wear, input signals that cannot be accepted by the computer, no output signal from the solenoid valve, rupture of mechanical hydraulic components, proportional linearity imbalance, hydraulic pressure drop, hydraulic leakage, Oil pump failure, hydraulic noise, circuit aging, abnormal sound, oil quality deterioration, power supply voltage drop, no output from the amplifier board, temperature out of control, etc. Different types of injection molding machines have different proportions of failure modes.
According to the form of failure, it can be roughly divided into electrical failure, action failure, process failure, mechanical failure, etc. The above classification is easy to search and analyze, and various faults may overlap with each other.